远场涡流内检测技术(RFT)在石油管道检测技术
介绍
远场涡流检测技术(最初称为远程场涡电流)在1951年由壳牌石 油开发公司W.R. MacLean发现并申请了专利保护,专利名为“一种利用磁技术测量铁质管线厚度的装置”。其第一次商业应用是在1959年用于油井套管检测设备。第一台RFT管线检测设备于1961年面世,也是由壳牌公司开发的。在国内远场涡流检测技术从90年代就开始广泛应用于石油天然气埋地管线的智能内检测, 远场检测器能使用在传统的超声和漏磁不能检测的工况。远场涡流检测技术(RFT)设备的优势在于其可以引发轴向磁场和 圆周方向的电场(涡电流)。由于其可以产生这样两种能量场,所以 RFT技术是唯一一种不需要其他辅助技术即可检测两种方向(轴向与 周向)缺陷的技术。
例如:
1、 内部有铁锈、结垢或是有比较严重的结蜡的管线。
2、含有弯曲半径较小弯头、三通和变径的管线。
3、 内衬管(水泥,高密度聚乙烯,黏土)。
4、 有结节情况的铸铁管线。
结垢和生锈严重的管
工作原理
远场涡流技术工作的原理是检测传感器发出的交流电磁场的变化。电磁场由传感器发出作用于金属管线,并在有金属损失的地方增强,电磁场被接收传感器接收,经模数转换器转换后由数字处理器进行处理。检测数据存储在检测器内。
下图形显示了激发线圈发出磁力线由接收线圈接收的过程:
下图形显示了幅值和相位关系:
远场涡流内检测优势
1、非接触无损检测。远场涡流不需要与管壁完全接触。
2、因为检测器的外径小和易弯曲的设计,远场涡流检测器能用于内径变化的管线和急剧弯曲的管线(例如三通)。
3、远场涡流检测器能检测到来自管线外侧的应力集中(例如凹痕或者岩石冲击)。
4、远场涡流检测器与管线是“软接触”,这样可以防止损伤管线内壁。
5、远场涡流检测检测电磁场相位与振幅的变化,提高了检测深度的准确性和对管线壁厚变化的敏感度。
6、检测器双向的设计能让检测器从同一管口进球并取球。
7、远场涡流检测器承压能力强,携带的传感器不易损坏。
运行管线常见腐蚀原因
二氧化碳腐蚀
硫化氢腐蚀
流态促进腐蚀
垢下腐蚀
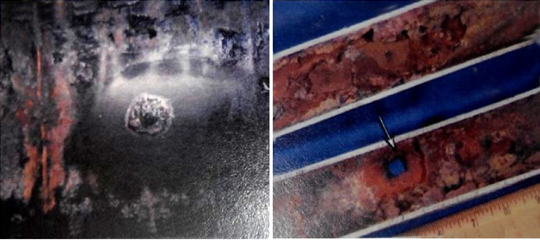
远场涡流数据
远场涡流检测器有密集的检测传感器,能体现出缺陷的时钟方向。这能增加缺陷的分辨率,即使检测器在管线内旋转也能检测出缺陷的准确的时钟方向。取得数据后,分析软件能提供管线壁厚的精确信息。
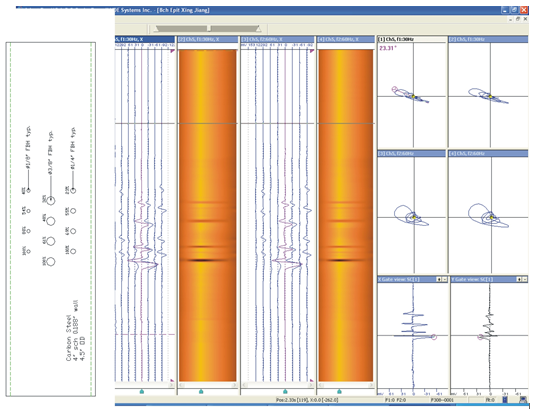
标样管测定
通过远场涡流检测器显示在管线的底部的局部壁厚损失(5:30钟点位置)
检测程序
远场涡流检测器收集并存储数据。检测器内部的电池能够完全给检测器供电,在管线中运行时不需要电缆供电。
对于较长的管线(高达30公里)最好的办法是从一端发射,从另外一端接收。在这种情况下,使用置于管线上方的地面标记来记录检测器通过的时间。使用GPS来定位的地面标记的地理位置。可以使用跟踪设备去监视检测器的位置。
由于远场涡流检测器易于弯曲和无需带缆的特性,能通过各种弯头。下面的图片是在两个90°的弯头上流安装的一个接收桶。
下图是探头原理图
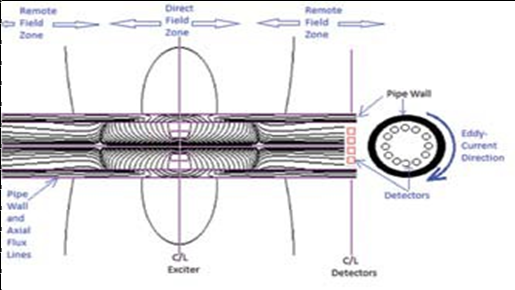
下图是适用于3英寸到48英寸钢管检测器图片
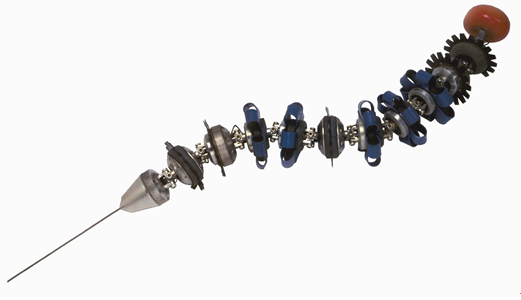
国内应用案例
目前,RFT技术在中国有了各种应用,如内衬管和低流速管的检测,及无法用其他ILI设备检测的管线。另外,RFT技术还具有其他一些优 势,使其成为一种非常有吸引力的替代技术,可以取代大家熟悉的 漏磁检测与超声波检测等成熟技术。其优势之一在于即可产生磁场 又可产生电场,两种场的传播方向呈90度角。上述能量场以不同的 方式与壁损缺陷相互作用,RFT设备的优势在于其对轴向缺陷和周向 缺陷都很灵敏。最成功的案例是2013年平湖油田海上平台立管检测。
海上平台立管